Here’s another relatively artistic project. I made this clock as a gift for someone:
The build was pretty straightforward. First, I searched online for mandala designs, and I started with one that I liked. The hardest part of this stage was finding designs that were 12-pointed; most mandalas have a 2^n number of points.
Next, I used Inkscape to vectorize the mandala and modified it to be appropriate for laser cutting. This included selecting parts to be engraved and cut as well as some tweaks to the design. I like making renderings to give me an idea of what the final project will look like, so I added some additional layers and a woodgrain bitmap to produce this preview.
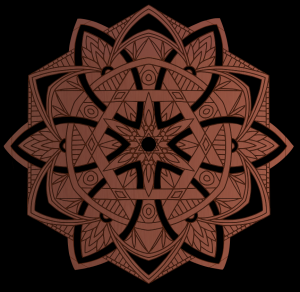
This image gives a picture as to what the mandala would look like before laser cutting; I could use the same technique to visualize other designs cut and etched in cherry wood.
Satisfied with the design, I purchased some 1/4″ cherry wood and lasered it out.
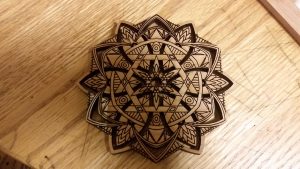
Before cutting, I covered the piece in masking tape to protect the finish. It was a pain to remove the masking tape from all the little regions, but the result looks good. You can still see a piece of tape on the piece in this picture.
I think settings on laser cutters always take some tuning, so, for reference, I used these settings on a 30W laser cutter.
- Cutting power: 100%
- Cutting speed 32%
- Cutting frequency: 2500Hz
- Raster power: 25%
- Raster speed: 100%
- Raster resolution: 500dpi
Next, I applied linseed oil to the result. I bought a small clock movement with brass parts, which I inserted into the hole in the face.